Space-saving solution for Verlarte
11/02/2014
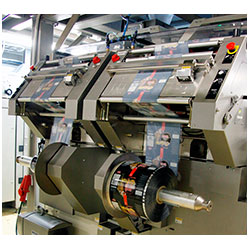
A compact snack-packing system from Ishida Europe has played an important role in enabling Spanish bread-based snacks manufacturer Velarte restructure a section of its factory to greatly improve return on floor space. At the same time, the new system has reduced product giveaway to just 0.75% of declared pack weight at speeds of up to 260 bags per minute.
Velarte’s Minut range consists of crisp squares of bread, with flavourings that include ham, cheese and tomato/oregano. The company had the capacity to manufacture this type of product at 400kg per hour. When it was decided to shift the emphasis to small pillow bags (30g) because of the popularity of smaller portions, it was clear that Velarte’s three existing weigher/bagmaker combinations would not be able to keep up.
The solution was to acquire an iTPS (Ishida Total Packaging System) consisting of an 18-head weigher mounted over twin Atlas bagmakers to replace all three of the older packaging systems. The fastest of the existing weighers was retained and put to work over a UVA bagmaker, filling Doypacks.
The 5m x 3m space where the three old weigher/bagmaker combinations had stood was converted to include not just the new weigher and bagmakers, but also the remaining older weigher and the doypack-filling machine. In addition, the area now includes a flavouring facility, the mainstream feed to the two weighers and a separate feed for chocolate-containing bread snacks, which are also packed by the ITPS into 30g bags.
Both the flavouring facility and the 18-head weigher are surrounded by temperature- and humidity-controlled cabins.
The Ishida CCW-R-218WB-D is a unique multihead model, specially designed to work with the two Atlas bagmakers. It resembles two 9-head weighers joined together in a kidney shape. The resulting geometry makes for maximum efficiency in getting compact doses of product into the bags at high speed.
The system is readily meeting its target speed of 260 bags per minute (i.e. 130 bags per bagmaker) for most products. Even the chocolate-containing products run at an impressive speed, thanks to the temperature and humidity control around the weigher.
Fill weights are coming within the range of 30.2g to 30.5g, so that giveaway is around 0.75% of declared pack weight. With a typical piece weight of 2-3g, and 10-15 pieces per bag, this represents a very high accuracy indeed, and a big improvement.
“Importantly for us,” says Salvador Matoses, Head of Engineering & Maintenance at the Velarte plant, “as well as being very fast, this system is much more accurate than the weigher-bagger combinations it has replaced.”
Salvador Matoses is also pleased with the Atlas bagmakers, which are delivering good quality seals, both end- and back seals. He likes the range of adjustments that can be made using the touch-screen, and the speed with which changeovers can be made and the system brought up again to full speed.
One very welcome feature is that the iTPS can carry on working during a product changeover. One side is stopped while the contact parts are taken off and cleaned by hand, while the other carries on delivering 130 bags per minute. Then the stopped side can almost immediately begin to work with the new product while the other side can be stopped and cleaned.
Cleaning is carried out by lifting contact parts off by hand, washing, air-drying and replacing on the weigher, the process being easily done in under half an hour, with the chocolate-containing products taking longest. The machine body is cleaned using an air hose and finished with a dust cloth.
Velarte generally works three 8-hour shifts. Moving from the old system to the new has halved the labour needed for weighing and bagging, allowing some staff to be redeployed to different parts of the factory.
The project to install the new equipment took place within a three-week window.
“We were making some very complex plans to maximise the use of the limited space available in our factory,” says Santiago De La Guardia Ricart, Plant Director. “Suppliers would need to co-operate closely, and above all be reliable. We felt that this equipment and the support offered by Ishida and its Spanish distributor CIMA would ensure there were no unforeseen problems.”
CIMA, based in Barcelona, fields a strong team of engineers and has built an excellent working relationship with Velarte.
“In the third week, we were already producing packed product,” says Santiago.
Santiago De La Guardia Ricart is pleased both with the overall project, which has given the company more options at a time when its factory space is limited, and with the performance of the iTPS.
“Our company’s marketing section is fast on its feet, taking much less time to respond to market changes than would a typical multinational. The least we could do was to provide a rapid manufacturing response to an urgent marketing need, in spite of the space constraints.
“We believed we could only pack these products efficiently on the Ishida iTPS, and its modest space requirements enabled it to fit neatly into our plans.”